Ingenious Strategies to Casting Aluminum: Keep Ahead
Ingenious Strategies to Casting Aluminum: Keep Ahead
Blog Article
Light Weight Aluminum Casting Providers Introduced: Vital Insights and Tips
Checking out the world of light weight aluminum spreading solutions can reveal a world of complex procedures and nuanced considerations that are crucial for effective end results. As we venture into the world of light weight aluminum casting solutions, prepare to reveal the essential aspects that can shape the trajectory of your jobs and boost your understanding of this complex craft.
The Basics of Aluminum Spreading
What essential procedures are entailed in aluminum spreading that create the foundation of this extensively made use of production strategy? Aluminum spreading is a affordable and functional technique utilized in various industries to produce complicated and detailed steel elements.
Trick aspects such as mold and mildew style, gating system, and cooling down price play a critical duty in determining the last high quality of the cast light weight aluminum component. The mold can be made from different products like sand, investment, or steel casting wax, depending upon the ins and out of the part and the preferred surface coating. After solidification, the mold is gotten rid of, and the spreading goes through completing processes such as warm machining, surface, and therapy coating to meet the called for requirements. Understanding these essential procedures is necessary for achieving high-grade aluminum castings with mechanical homes and specific dimensions.
Various Casting Techniques Described
Checking out the numerous strategies used in light weight aluminum casting uses valuable understandings right into the varied methods utilized to attain specific and detailed steel parts. One common approach is sand casting, where a mold and mildew is developed utilizing compacted sand around a pattern of the desired part. This strategy is economical and functional, suitable for both simple and complicated shapes. An additional technique, pass away spreading, includes injecting liquified aluminum right into a steel mold and mildew under high stress. Die casting allows high accuracy and repeatability, making it optimal for mass manufacturing of tiny to medium-sized components. For more detailed styles, financial investment casting is commonly chosen. This approach utilizes wax patterns that are melted away, leaving a dental caries for the molten light weight aluminum to load. Financial investment casting returns exact information and smooth coatings, making it preferred in sectors like aerospace and auto. Each casting technique has its unique advantages and is picked based on variables such as expense, complexity, and volume factors to consider.
Factors to Think About When Picking a Company
When choosing an aluminum spreading provider, examining their experience and expertise is essential for making sure quality and integrity in the production procedure. The copyright's experience in the field suggests their familiarity with different spreading strategies, prospective obstacles, and finest methods. It is important to make inquiries regarding the kinds of tasks they have worked with in the past, guaranteeing they align with the intricacy and specifications of your own task.
Furthermore, think about the service provider's online reputation within the industry. Search for testimonials, testimonials, and study that demonstrate their ability to provide high-quality aluminum castings continually. A credible provider will commonly have certifications or affiliations with industry companies, showcasing their commitment to quality and adherence to sector standards.
Additionally, examine the service provider's capacities in regards to customization, quantity needs, and project timelines. Guarantee that they can fit your specific requirements and have the adaptability to range manufacturing as called for. Efficient communication and transparency concerning expenses, lead times, and quality assurance processes are also vital aspects to consider when picking a light weight aluminum spreading service supplier.
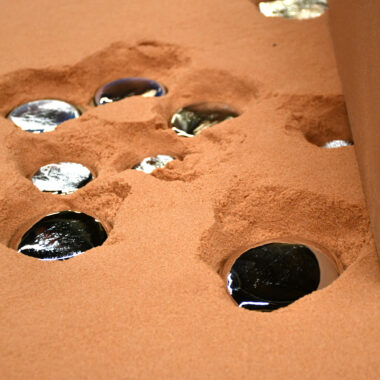
Common Obstacles and Solutions
Browsing through the complexities of light weight aluminum spreading procedures often offers manufacturers with a collection of obstacles that require ingenious services to make certain efficiency and high quality in manufacturing. One common difficulty faced in light weight aluminum spreading is the formation of issues such as porosity, shrinkage, or additions as a result of incorrect mold and mildew design or insufficient metal top quality. These defects can compromise the architectural stability of the end product. To address this, suppliers ought to perform comprehensive simulations and tests to enhance the spreading procedure parameters and ensure the quality of the molds and products made use of.
One more challenge depends on accomplishing exact dimensional precision, especially for intricate geometries. Variants in cooling prices, mold expansion, and product homes can bring about deviations from the designated dimensions. Applying innovative innovations like computer-aided design (CAD) and computer numerical control (CNC) machining can improve accuracy and consistency in aluminum spreading. In addition, preserving correct control over the melting and pouring procedures is essential to prevent concerns like overheating or unequal circulation of the liquified metal - casting aluminum. By purchasing automation and real-time tracking systems, suppliers can enhance process control and reduce variants, ultimately improving the overall top quality of aluminum cast products.
Tips for Optimizing Your Spreading Projects
By making sure that the gating system is well-designed and correctly placed, you can boost the circulation of molten light weight aluminum and reduce the opportunities of flaws in the final spreading. Additionally, making use of computer system simulations can assist in predicting and assessing the flow of metal throughout the casting procedure, permitting for adjustments to be made before actual manufacturing starts.

Final Thought
To conclude, recognizing the fundamentals of aluminum casting, various casting techniques, variables to take into consideration when selecting a copyright, common difficulties and services, and tips for enhancing spreading tasks are vital for successful results. By adhering to these understandings description and implementing ideal organizations, techniques and individuals can make certain efficient and effective light weight aluminum casting services that meet their specific needs and requirements.
Comprehending these essential procedures is crucial for attaining top notch light weight aluminum castings with precise dimensions and mechanical residential or commercial properties.
When choosing an aluminum casting solution supplier, reviewing their experience and proficiency is important for making certain top quality and integrity in the production process. Effective interaction and openness relating to expenses, lead times, and quality control processes are additionally vital elements to take into consideration when selecting an aluminum spreading solution provider.
Browsing via the intricacies of light weight aluminum spreading processes usually presents manufacturers with a series of challenges that need ingenious remedies to make sure effectiveness and top quality in manufacturing. One usual difficulty faced in light weight aluminum casting is the formation of problems such moved here as porosity, shrinkage, or incorporations due to incorrect mold design or insufficient metal quality.
Report this page